Learn how to build high-quality DIY acoustic panels for a fraction of the cost of store-bought acoustic panels.
If you’ve managed to put together IKEA furniture before, you’ll be able to build your own acoustic panels. This guide will show you how to build 24-1/2” x 48-1/2” acoustic panels that you can use to sound-treat your home studio.
Tool and Material Costs
From a cost perspective, you’ll need to build a handful of acoustic panels to save money going the DIY route. The more panels you build, the more cost-effective it is to build panels, as opposed to buying them pre-made.
Shipping costs are something you need to keep in mind when looking at store-bought panels. Depending on how many panels you buy, shipping costs can almost double the price.
List of Required Tools
Lots of DIY acoustic panel build guides out there provide unrealistic tool and material costs. They either assume you have all the tools you need, or neglect to factor in small materials costs that add up.
I want to provide you with a realistic cost assessment, so I’ve included every possible tool and material that you might need. There’s a chance that you already have access to some of the following tools, which will drop the price down even lower.
Minimum Total Price: $241.38
Use this link to quickly add the tools from this list to your Amazon cart.
List of Required Materials
Material costs are scalable, meaning that if you want to build more than 6 panels, you can simply buy more materials. Once you have the tools you need, you’re looking at spending about $33.83 per panel or less.
Minimum Total Price for 8 Acoustic Panels: $270.66 ($33.83/panel)
Use this link to quickly add many of the materials from this list to your Amazon cart.
Project Completion Time
Beyond the cost of this project, you need to take into account the time investment. If you plan to build these acoustic panels by yourself, it’s probably going to take a few days.
Most people reading this guide likely enjoy DIY projects, want to remain budget-conscious, and are looking for a fun weekend activity. However, if you make a killing at your day job and don’t like building things, it may make more sense to just buy store-bought acoustic panels.
1. Cutting the Wood
The first thing you need to do is cut up a 3/4” thick 4’ x 8’ piece of plywood. Lots of plywood comes in a 23/32” thickness, which is fine as well. The missing 1/32” won’t make a significant difference when assembling the panels.
When you go to Home Depot to purchase your plywood, ask an employee to cut the 4’ x 8’ piece of plywood into four separate pieces. This will allow you to fit the plywood pieces into your car and cut them down to size at home. Home Depot won’t cut plywood to less than 8” wide, which is why you’ll need a circular saw.
Note: Do not purchase MDF board instead of plywood, even though it’s slightly cheaper. Home Depot won’t cut MDF board for you because the particles it produces can cause respiratory issues. You shouldn’t cut MDF board yourself either for the same reason.
Print off the following image and hand it to a Home Depot employee so they know how to correctly divide your plywood sheet. The width of the blade they use to cut the panels will make each section slightly smaller than noted, as will cutting the panels down further with your circular saw. The plywood strips may end up just shy of 3” wide, but it shouldn’t affect your ability to pack the acoustic panels with the insulation being used later on.
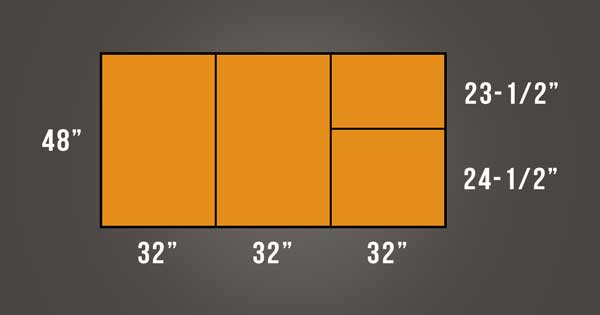
From one sheet of plywood, you’ll be able to cut the plywood strips you need for 9 acoustic panels. You can cut eighteen 47” x 3” plywood strips from the two larger plywood sheets, and eighteen 24-1/2” strips from the remainder of one of the larger plywood sheets and the two smaller plywood sheets.
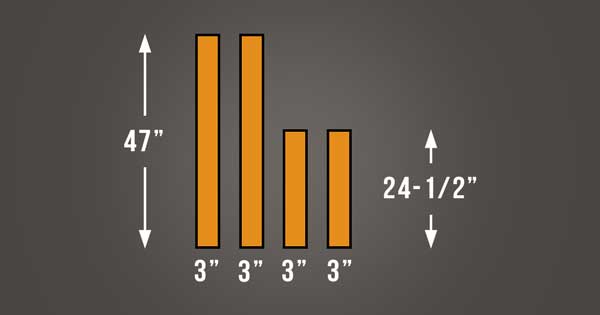
The smaller 24-1/2” strips will cap off the ends of the longer plywood strips, adding 3/4” to the top and bottom of your wooden assembly. The height of the frames will end up at 48-1/2” tall.
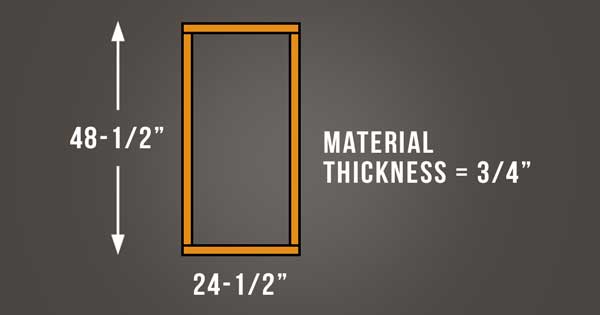
The inside of the frame measures in at 47” x 23”, which is the perfect size for the ROCKWOOL SAFE n SOUND insulation being used. Each bag of SAFE n SOUND contains 8 units of 3” thick, 47” x 23” insulation.
2. Assembling the Frames
To assemble the frames, you’ll need a drill, a countersink drill bit set, a speed square, wood screws, and some wood glue.
A countersink drill bit will create a pilot hole that will help prevent the wood from cracking when you install the screws. It will also create a divot in the wood for the screw heads to rest in, making sure they sit flush with the surface of the frame.
Use your speed square to mark 4 holes on the face of your 24-1/2” plywood strips. Each one of these holes will be offset 3/4” from the long side of the strip, and 3/8” from the short side.
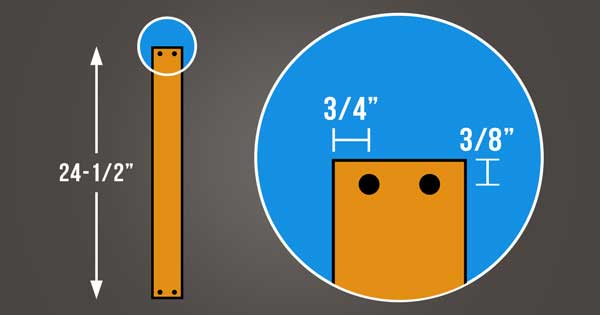
Your 47” plywood strips will require two pilot holes centered on each end. Offset the holes 3/4” from each side so that they align with the holes in your 24-1/2” plywood strips.
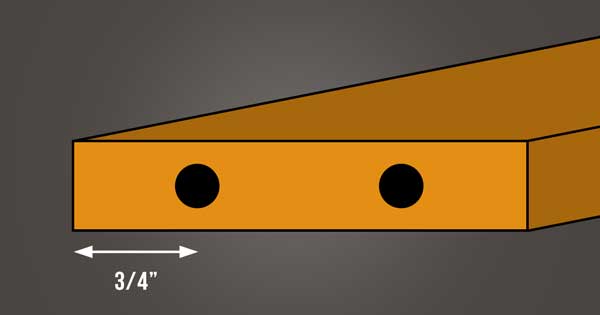
Apply a bead of wood glue to the end of your 47” plywood strips right before you screw them together with the 24-1/2” plywood strips. The wood glue will strengthen the final product. Wipe up excess wood glue with a cloth to avoid making a mess.
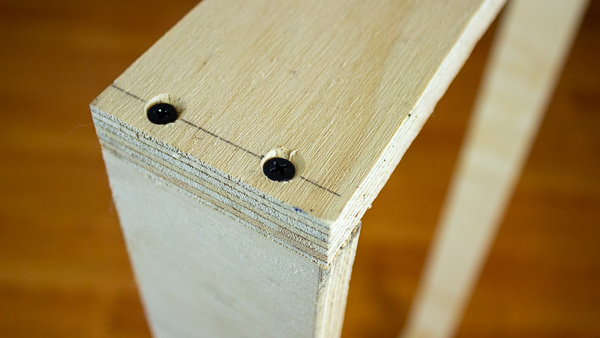
Repeat this process until you’ve finished assembling all of your frames.
3. Adding Support Strips
You can add two optional support strips to brace the inside of your frames if you’d like; if you have excess plywood it’s certainly a good idea.
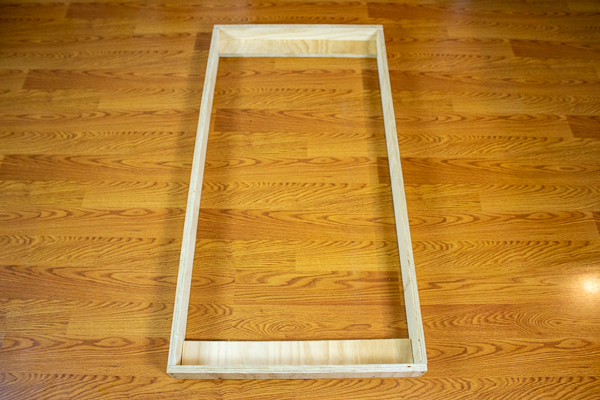
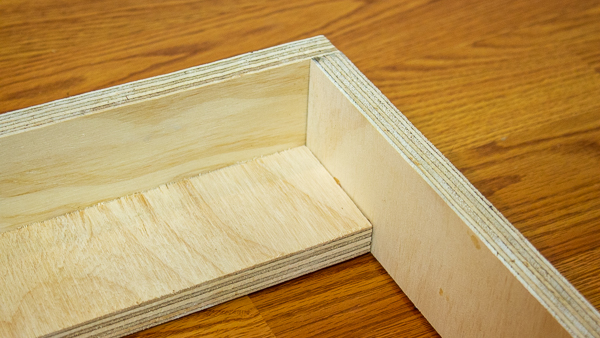
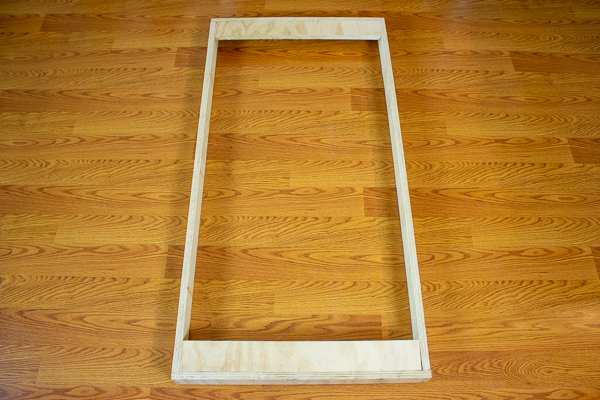
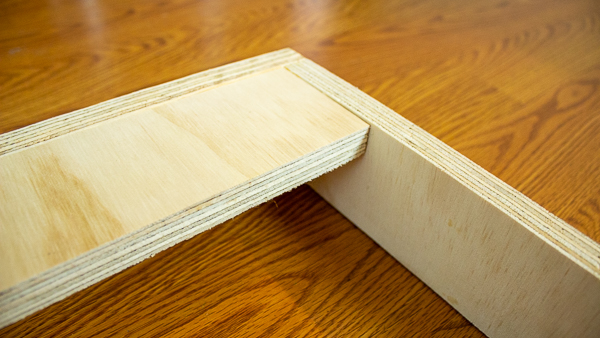
The support strips will be roughly 23” x 3”, but you should measure the empty space on the inside of your frames to ensure a tight fit.
To make the following steps easier, consider using a pair of clamps to hold your support strips in place while you drill the pilot holes. Apply a bead of wood glue to the parts of your plywood strips that will contact the frame before installing your strips using wood screws.
Measure 4-3/4” inward from the long side of your frames and drill a pilot hole into the face of the plywood strips capping off the frames. These holes should sit back 3/8” from the edge facing upward. These screws are meant to fasten the support strip into place.
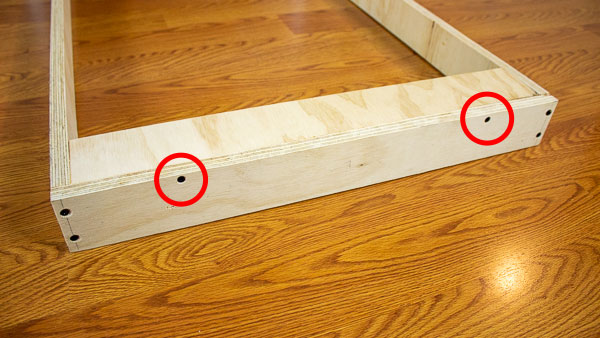
To stabilize the support strips further, add another screw on each side of the frame, aligned with the center of the support strips. If you measure 2-1/4” from the top of the short face of the frames,
The 2-1/4” measurement takes into account the 3/4” thickness of the plywood cap on top of the frame, and half the width of the support piece (1-1/2”). When you drill your pilot hole, it should align perfectly with the center of the support strip’s short edge.
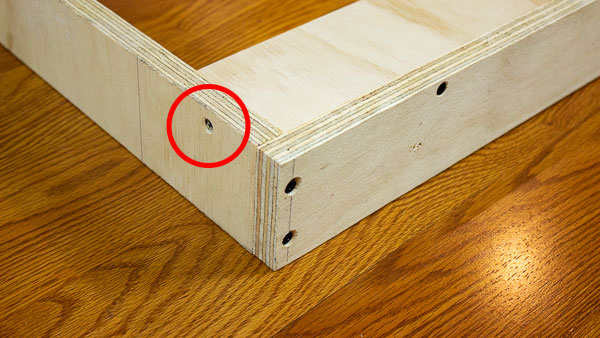
4. Installing the Insulation
You’ll be using fiberglass screen to keep the insulation in place. Roll a length of screen over the back of your panel (the side with the support strips), staple the screen into place, and then cut it down to size. Pull the screen tight as you staple it to prevent your insulation from slouching later on.
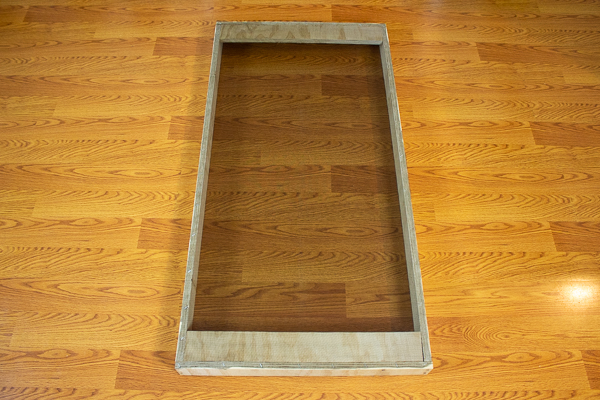
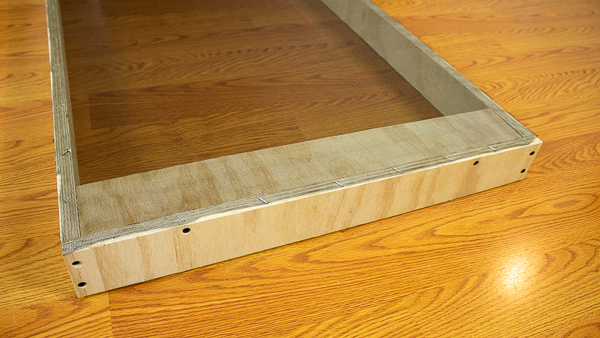
Hammer staples that sit proud of the surface into the frame. You don’t want staples pushing through the fabric when your wrap your acoustic panels.
Before installing the screen on the other side of the frame, you’ll need to fill the frame with insulation. If you’re not using support strips, you don’t need to modify the insulation in any way. You can drop the insulation directly into the cavity of the frame and it should fit perfectly.
If you’re using support strips, you’ll need to make a cutout in each side of the insulation to accommodate the thickness of the support strips. The cutouts should be roughly 23” x 3” and 3/4” deep.
Note: When handling insulation, wear a mask, gloves, and long-sleeves.
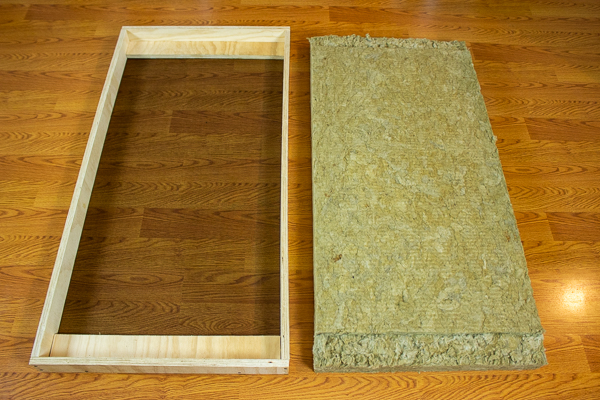
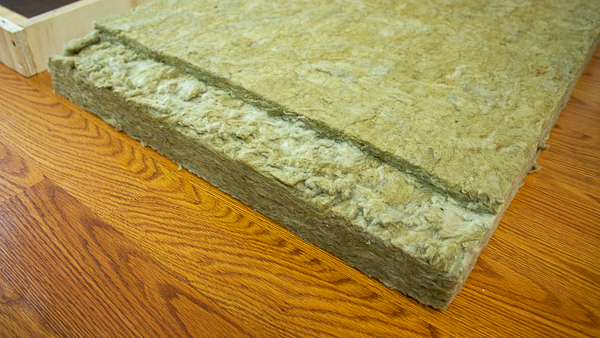
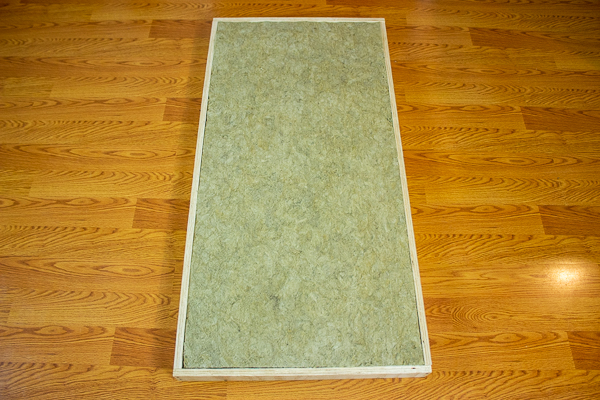
Cover the front side of the frame with fiberglass screen and staple it into place. The insulation is now held in place by fiberglass screen on both sides.
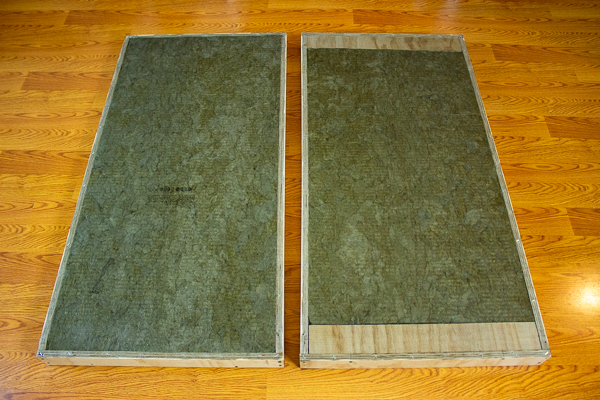
5. Wrapping the Acoustic Panels
At this point, you could use the panels as they are, but they don’t look great yet. You’re going to wrap them in fabric using adhesive spray.
The fabric you use will affect the absorption coefficient of your panels. Guilford of Maine is the fabric that most people prefer to use for acoustic panels, but felt costs much less and will also work. What’s important is that sound is able to pass through the fabric so that it may be absorbed by the insulation.
You can get creative with fun fabric designs if you like. In general, lighter colors will make your studio feel more spacious. I personally chose to wrap my ceiling panels in white felt, and my wall panels in light grey felt.
The fabric you buy will need to be at least 36” wide to span the width and sides of your panel (24” + 3” + 3”). You’ll end up with about 3” of excess material on each side to pull the fabric tight. The more excess fabric you have to work with, the easier it will be to wrap the panels.
To cover the length of one panel, you’ll require 60” of fabric; this takes into account the length of the panel, the top and bottom edges, as well as 3” of excess material to pull the fabric tight.
Each panel will require a rectangle of fabric that’s 36” x 60”.
Lay down the fabric on a clean and hard surface. Center your panel on the piece of fabric. Coat one of the long edges of the panel with adhesive spray and adhere the fabric to it. Allow the edge to dry and then adhere the fabric on the opposite side of the panel to the frame as well.
Note: To avoid wrecking the surface you’re working on with adhesive spray, lay down a piece of cardboard under your work area.
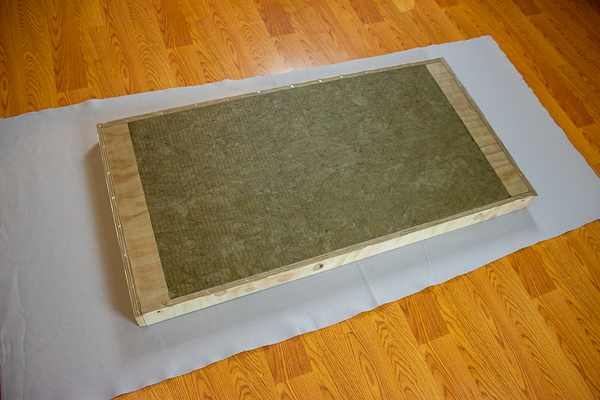
Pull the fabric REALLY tight to avoid wrinkles. Once the adhesive has dried, you’ll need to completely remove the fabric and re-wrap your panel with new fabric if you didn’t get it right the first time.
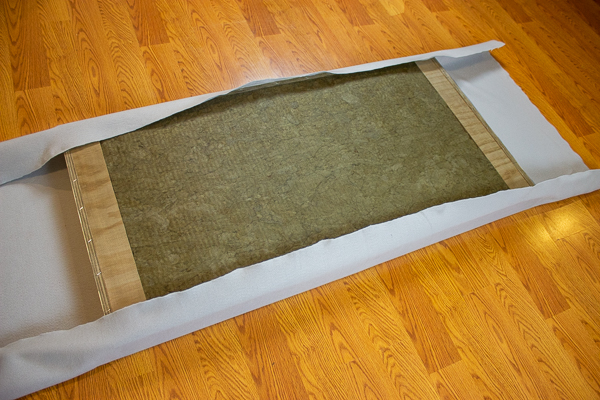
Trim away the excess fabric along the sides that you just adhered to the frame.
You’ll need to add 4 relief cuts to the fabric to avoid it having it bunch together when you fold over the ends.
Spray adhesive along one of the remaining uncovered edges, and adhere the fabric to it. Pull the fabric tight and do the same thing for the last remaining uncovered edge. Trim away the excess fabric.
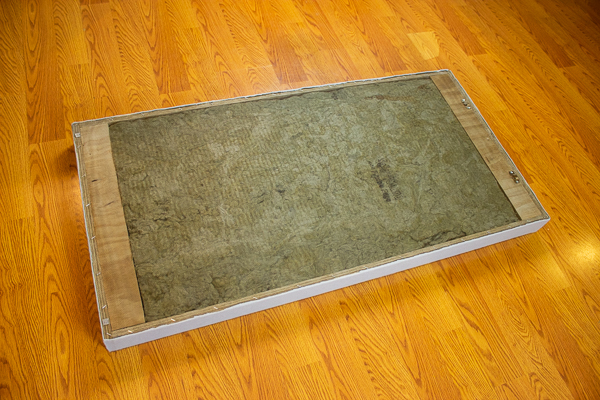
When you flip your acoustic panel over, you should have a wrinkle-free product.
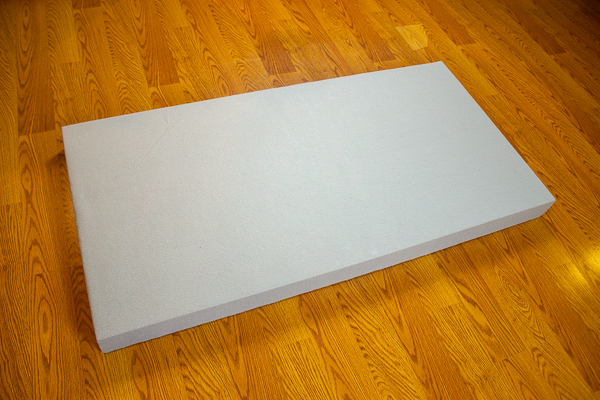
If you’ve used a thinner or lighter material to wrap your panels, you might be able to see the frame through it. Once the adhesive has dried, you can wrap your panels a second time to hide the frame.
Option 1 – Wall-Mounting Your Acoustic Panels
Your panels are almost done, but you still need to be able to wall mount them. I’ve found that using a couple pairs of flush mount brackets will get the job done effectively. Installing the brackets requires some rather precise measurements, but the tradeoff is that you’ll be able to hang five panels for around $9.
Drill two pilots holes 10-1/2” apart, centered on the back of your panels. You can drill these holes directly into the support strips, or if you’re not using support strips, directly into the top of the frame. Make sure that the brackets are facing downward so that they can hook onto the upward-facing wall brackets.
Screw the brackets into place using screws with heads that sit flush with the brackets. You’ll probably need to make a trip to the screw isle at Home Depot, with your brackets, to find screws that work. While you’re there, pick up a package of drywall anchors that the screws will fit into. It’s a bit of a risk ordering screw online because you don’t get to see how they fit before you buy them.
The left hole of the right-side bracket should receive a screw, as should the right hole of the left-side bracket. Add another screw to each bracket to fasten it into place.
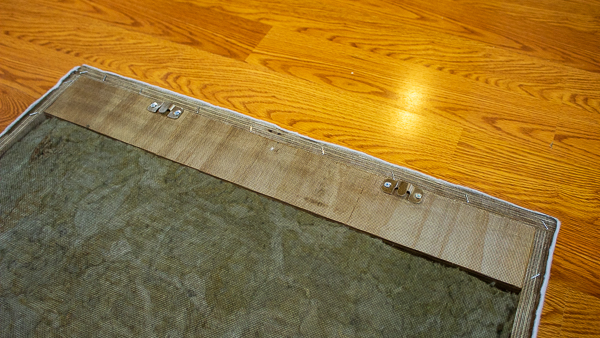
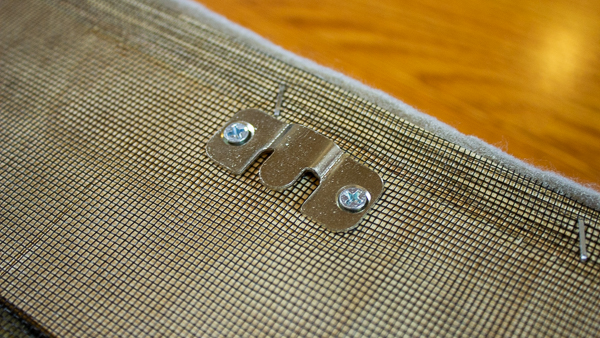
With your panel facedown on the ground, attach an adhesive furniture bumper to the bottom corners of the panel. You can stick these bumpers directly onto the fiberglass screen. The bumpers will keep your panels parallel with the wall when you wall-mount them.
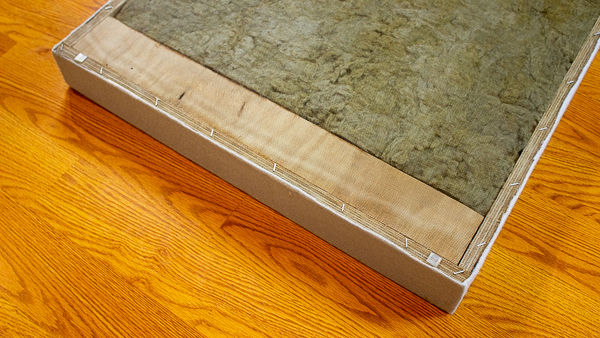
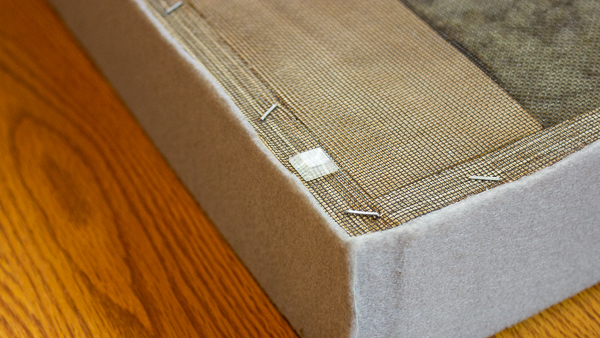
On your wall, mark out a distance of 10-1/2” and install your drywall anchors. Screw the brackets into the drywall anchors. Make sure that these brackets are facing upward so that you can hook the panel brackets onto them.

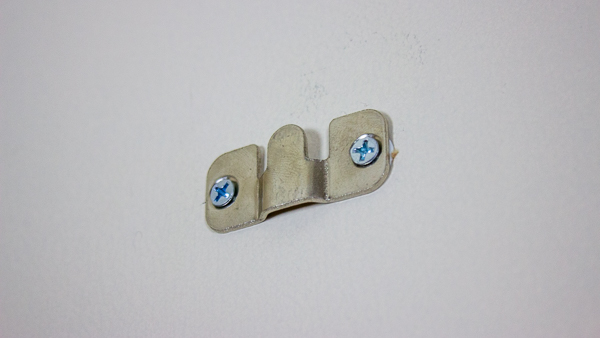
You don’t have much wiggle room here, so you need to ensure that your measurements are tight. It can be a little tricky to line up the brackets on the back of the panel with the brackets on the wall; mainly because the brackets are hidden as you do this. Be patient and you’ll eventually feel the acoustic panel lock into place.
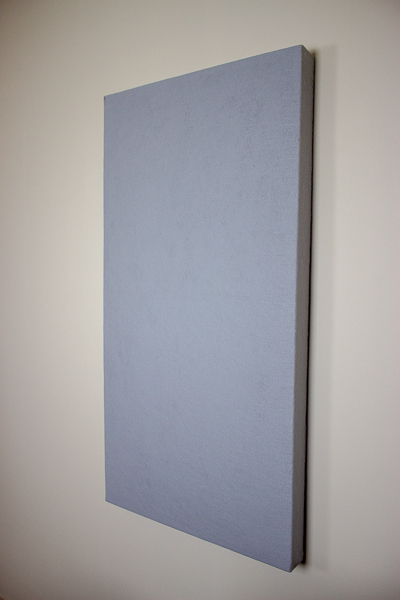
Refer to “The Ultimate Acoustic Treatment Guide for Home Studios” if you’re unsure where you should place your acoustic panels within your studio.
Option 2 – Ceiling-Mounting Your Acoustic Panels
To prevent first reflections from causing comb filtering, you’ll need ceiling-mounted panels above your listening position. Ceiling-mounting panels will require drywall anchors, screw eye hooks, carabiners, and some chain.
Install a screw eye hook into each corner of your ceiling-mounted acoustic panel. Make sure that the screw eye hooks are spaced uniformly. The following dimensions should work well if you’ve installed support strips.
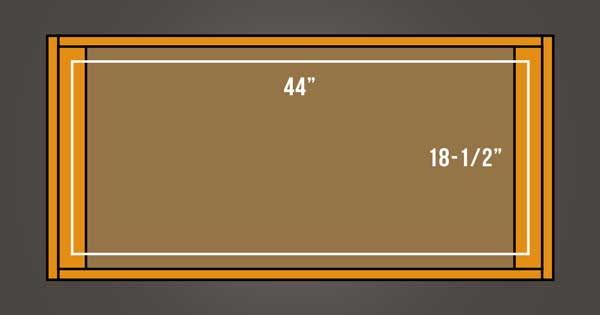
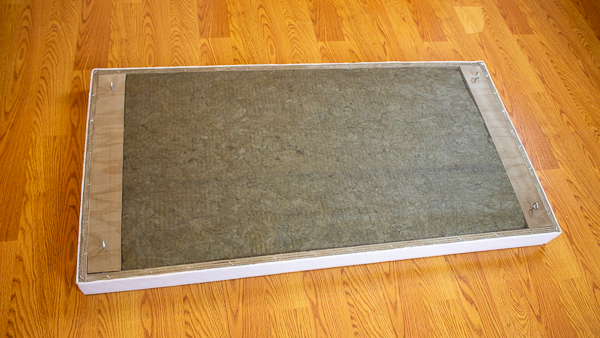
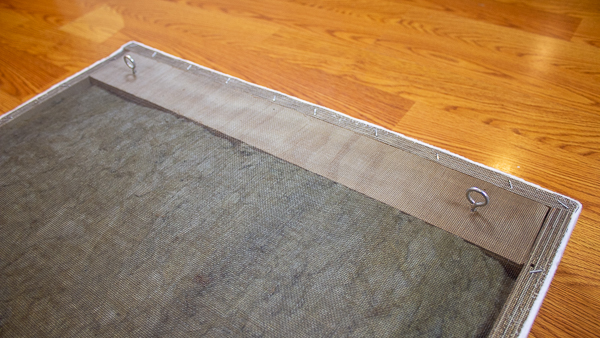
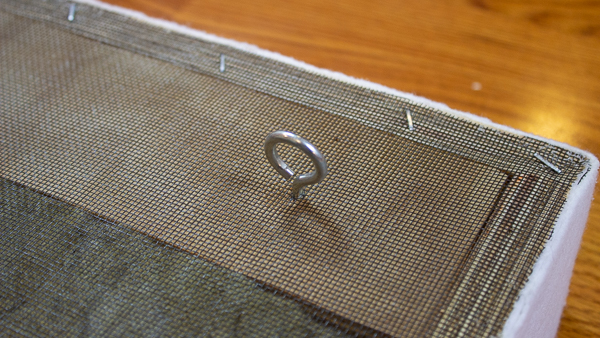
If you didn’t use support strips, screw the screw eye hooks directly into the frame of your panel. The 44” measurement should end up somewhere closer to 47-3/4”.
Install drywall anchors into your ceiling, mirroring the positioning of the screw eye hooks you installed in your acoustic panels. Using a laser level will make marking your ceiling a bit easier.
If the screw eye hooks are a different size than the screws you used to attach your flush mount brackets to the wall, you’ll need to use bigger/smaller drywall anchors for this step.
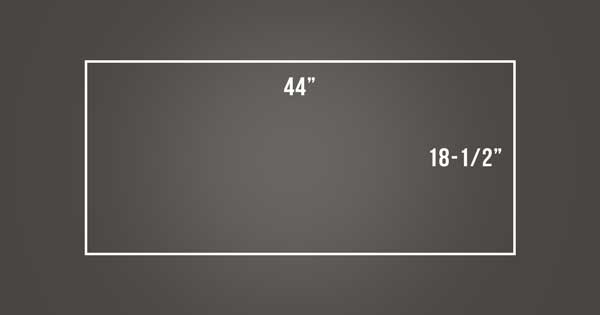
Screw a screw eye hook into each drywall anchor and attach a carabiner.
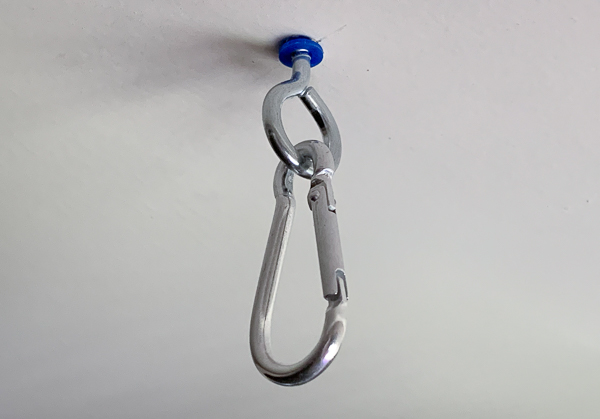
You may want to buy your screw eye hooks and drywall anchors in-store so that you can ensure the screw eye hooks fit into the drywall anchors.
To provide an air gap between your ceiling and panels, which will increase effectiveness, you can suspend the panels using some chain from an art supply store. Use a pair of pliers to add or remove chain links as necessary. Attach another carabiner to the dangling end of the chain.
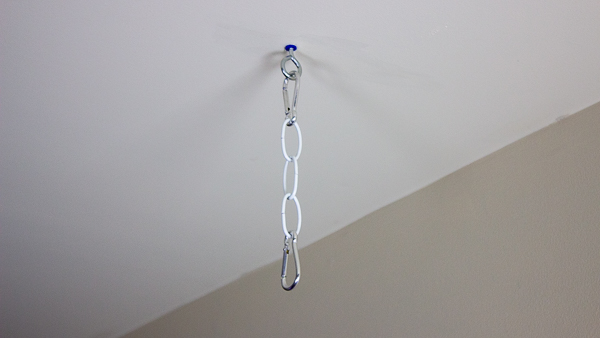
Clip the screw eye hooks on one end of your panel into two of the hanging chain assemblies.
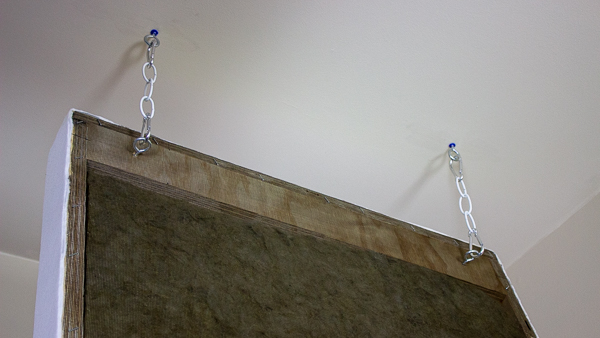
The drywall anchors should be able to temporarily support the weight of the acoustic panel as you attach the other side of the panel to the ceiling. Just to be safe, you may want to get a friend to support some of the panel’s weight as you clip it into place.

The suspended acoustic panel should hang parallel alongside the other panels you’ve ceiling-mounted, if any.
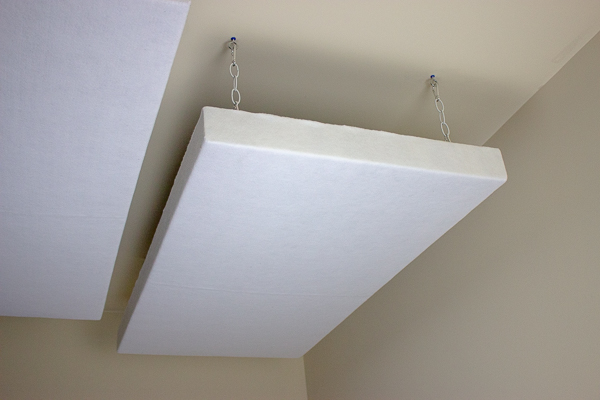
Building Bass Traps
Building your own acoustic panels gives you full customization over the product. 3” panels will absorb midrange effectively and work well when positioned to absorb first reflections around your listening position. However, to adequately absorb bass, you’ll need to build panels that are at least 4” thick.
By doubling up on insulation, you can create 6” thick acoustic panels that are super effective at absorbing bass; these panels will do very well on the rear wall of your studio and help reduce low-end standing waves.
To make 6” thick acoustic panels, you’ll need to cut plywood strips that are 6” wide instead of 3″ wide; this will allow you to build frames that are 6″ deep. You’ll also need to use more fabric when you wrap the panels.
More Ways to Save Money
Rockwool Acoustic Mineral Wool Insulation is by far one of the most expensive materials on the list. You can save up to 30% on insulation if buy in bulk from Home Depot. You’ll need to buy at least 15 bags of insulation to get this deal. Consider purchasing insulation with a group of friends that also want to build acoustic panels to save more money.
Looking for another fun DIY project? Learn how to build a vocal booth for under $85.
Make sure to follow Black Ghost Audio on Facebook, Twitter, Instagram, and YouTube to stay up to date on the latest music production tips and tricks. There’s new content every week.